Do you have a product idea?
Let’s have a meeting and discuss your plans, years of experience help us catch design or manufacturing-related problems ahead of time. We will discuss the various aspects and options that are available. Our CAD design team will draw up your product ready for the mould to manufactured. it’s worth noting that a quality mould produces quality products repeatably. Complex shapes are CNC machined from an aluminium billet, while larger straight forward shapes can be fabricated from sheet steel. Once your moulding tool has been produced, test products will be moulded and presented for approval.
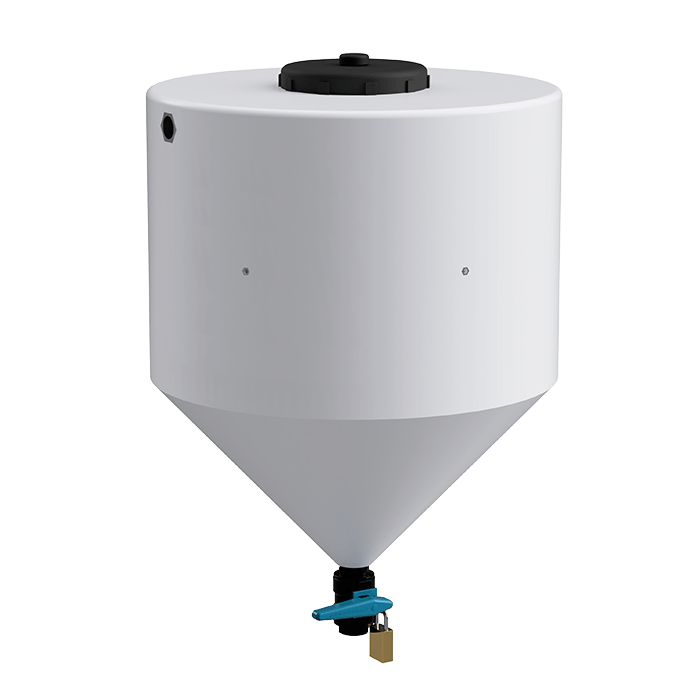